Apporter toujours plus de valeur aux clients et éliminer les activités qui n’en apportent pas : voici comment nous pourrions résumer le Lean Management. Mais attention, loin d’être un tour de magie, le Lean Management est une démarche structurée qui peut impulser un développement important au sein de l’entreprise. Voyons pourquoi et comment.
Le client est la partie la plus importante de la ligne de production.
Le Lean Management en bref
« Lean », qui pourrait se traduire par « maigre » en français, est le nom qui a été donné à la méthodologie créée par Toyota au Japon dans les années 70, au sein de ses usines, et qui pouvait alors se définir comme une gestion sans gaspillage. Même s’il a été initialement déployé dans l’industrie automobile, le Lean Management est une philosophie qui peut bien sûr être appliquée à tous les types d’organisation et dans de nombreux secteurs d’activité.
Il s’agit avant tout de rechercher la performance grâce à l’amélioration continue dans le but de satisfaire le client en améliorant la productivité, la qualité, les délais et les coûts. Pour cela, le Lean Management s’appuie sur 4 piliers : le travail en équipe, la communication, l’utilisation efficiente des ressources et l’élimination des gaspillages.
Bien plus qu’un simple outil, le Lean Management s’attaque de façon systématique à la résolution active des problèmes de production à différents niveaux dans l’entreprise :
- L’élimination de la surproduction,
- La diminution des stocks,
- La réduction des délais,
- La maîtrise des coûts,
- L’optimisation du transport,
- La maximisation des compétences,
- L’optimisation de la communication,
- L’amélioration de la qualité.
En résumé, le Lean Management permet de fournir un travail hautement qualifié dans des conditions idéales de fonctionnement avec un minimum de temps, de ressources et d’énergie dépensés. Il s’agit d’apporter plus de valeur au client tout en éliminant les activités qui n’en ont pas.
Lean Management : par où commencer ?
Même si on entend beaucoup parler du Lean Management et qu’il est déployé un peu partout, cela n'est pas toujours évident de savoir comment adapter la démarche à son propre contexte. Les principes sont simples et les gains évidents, mais comment démarrer ?
Une étape initiale est indispensable : changer d’état d’esprit ! Les méthodes classiques ne fonctionnent plus et il est vital de changer de paradigme car la richesse de l’entreprise, c’est avant tout le savoir et l’expertise qui existent au sein de l’organisation entière, de la direction générale jusqu’aux opérationnels.
Une fois ce cap passé, il est important de bien comprendre que même si le Lean est lié à de nombreux outils performants tel que le Lean Six Sigma et la méthode DMAIC, le Kaizen, la méthode des 5S ou le Kanban pour ne citer qu’eux, il est bien plus qu’un simple outil supplémentaire et correspond davantage à une philosophie. Il conviendra donc de l’aborder en suivant quatre étapes incontournables :
- Identifier les besoins business de l’entreprise,
- Identifier le potentiel d’amélioration opérationnelle,
- Évaluer la capacité de changement,
- Dresser le plan d’action.
1Identifier les besoins business de l’entreprise
Il s’agit de comprendre ce qui fait la valeur du produit ou du service de l’entreprise, son positionnement par rapport aux concurrents, sa promesse au client. À partir de là, on pourra analyser les besoins d’amélioration, du point de vue de la qualité, des coûts et des délais. Il est alors important de ne pas négliger les contraintes extérieures qui pourraient influencer les actions.
2Identifier le potentiel d’amélioration opérationnelle
Outre les besoins business, il faut comprendre le potentiel d’amélioration opérationnelle. Il est temps d’identifier sur le terrain les gaspillages, en ayant une démarche d’analyse sur les différents indicateurs opérationnels : taux de service, efficacité des équipes, délais de processus de production, etc. Les différents gains potentiels doivent être chiffrés précisément si l’on veut pouvoir les décliner en objectifs mesurables. Le « Gemba Walk » (inspiré du mot japonais « genba » qui signifie « là où se trouve la réalité ») est particulièrement adapté à cette phase puisqu’il consiste à parcourir l’usine ou l’atelier pour mener un audit et prendre conscience de ce qui s’y passe concrètement pour les opérationnels qui sont au cœur de la création de valeur.
3Évaluer la capacité de changement
Dès lors que la nécessité et les potentiels d’amélioration sont identifiés, il reste bien sûr à comprendre comment tout cela va pouvoir s’articuler. Quelle est la capacité de changement de l’organisation ? Combien de temps prévoir pour le déploiement de ces améliorations ? Quels sont les freins et les accélérateurs présents au sein de l’organisation ? Autant de questions auxquelles il faut répondre avant d’engager la dernière phase…
4Dresser le plan d’action
Pour être pérenne, la transformation doit s’accompagner de plans d’action opérationnels. Aborder l’amélioration continue de manière structurée, systémique et cohérente : voilà les clés du succès.
D’ailleurs, si vous souhaitez connaître toutes les bonnes pratiques pour réussir vos plans d’action, n’hésitez à pas à télécharger notre ebook :
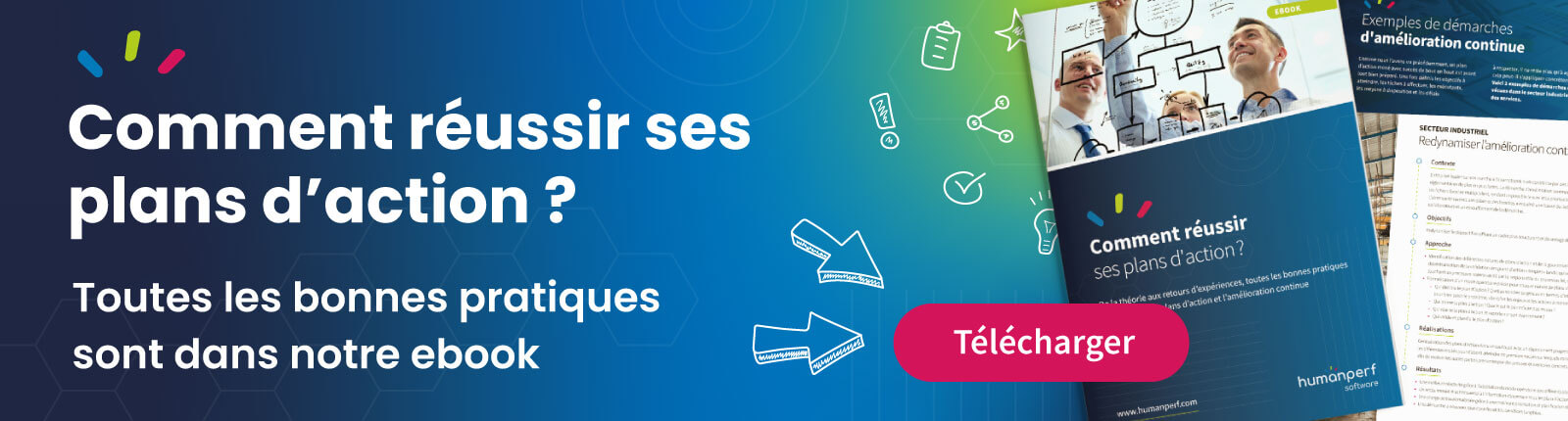
Les véritables atouts du Lean Management
La méthode a été utilisée et éprouvée depuis sa création dans les années 70. Promue par les plus grands cabinets de conseil qui vantaient les perspectives d’augmentation de la productivité, elle apportera systématiquement quatre grands avantages :
- Instaurer une démarche pérenne : le Lean Management se pense à long terme, il ne s’agit pas de trouver une solution d’urgence à la rentabilité immédiate.
- Favoriser une organisation stable dans l’entreprise : le Lean crée de facto une fidélité des clients et des salariés ; les deux étant au cœur de la création de valeur dans l'entreprise.
- Lutter efficacement contre le gaspillage et ce, à tous les niveaux (fabrication, management, commercialisation).
- Faciliter la digitalisation de l’entreprise : en effet, en pointant du doigt les tâches à faible valeur ajoutée, les redondances hiérarchiques, l’amélioration de la relation client/fournisseur/salarié, le Lean pousse naturellement à dématérialiser et à automatiser de nombreuses tâches.
En quoi le Lean est-il différent des autres méthodes d’amélioration continue ?
Le Lean Management contribue à « mieux travailler ensemble ». Le manager Lean ne cherche pas seulement à faire en sorte que ses équipes s’améliorent mais cherche à comprendre, avec les équipes, ce que mieux travailler signifie dans leur contexte spécifique.
Le Lean Management permet donc une amélioration durable et rentable des processus de l’organisation, c’est aussi pour cette raison qu’il tient toutes ses promesses en matière d’amélioration continue.
À l’instar d’autres méthodes qualité, le Lean Management a finalement été quelque peu galvaudé. Pourtant, bien utilisé, c’est-à-dire en plaçant le client et le collaborateur au cœur des priorités, il demeure une des philosophies les plus puissantes pour pérenniser une croissance qui soit réellement créatrice de valeur.
Pour aller plus loin, n’hésitez pas à lire notre article : Amélioration continue, le guide pour bien gérer la démarche.
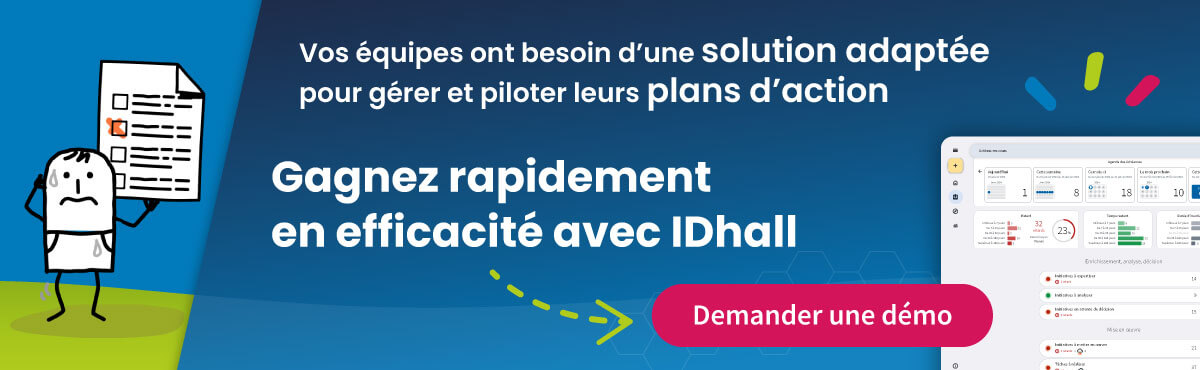