Au cœur du Lean Management, la méthode 5S fait partie de la boite à outils Qualité idéale pour contribuer à la démarche d’amélioration continue dans les organisations. Cette méthode d’organisation japonaise s’est largement diffusée au sein du monde industriel après sa mise en œuvre initiale par Toyota, mais elle peut s’appliquer aussi bien à un atelier qu’à un bureau.
L’objectif à atteindre est simple : mettre de l’ordre dans son environnement de travail et ses matériels pour davantage d’efficacité et de sécurité.
La méthode 5S : définition
La méthode des 5S part du postulat que la réalisation d'un travail efficace et de qualité nécessite un environnement propre, de la sécurité et de la rigueur. Les 5 S représentent donc 5 actions à mettre en œuvre dans son espace de travail :
- Seiri : Supprimer l’inutile.
- Seiton : Situer et ranger les choses.
- Seiso : (faire) Scintiller et nettoyer.
- Seiketsu : Standardiser les règles.
- Shitsuke : Suivre et progresser.
Nous avons repris ici l’appellation utilisée notamment par Christian Hohmann dans son ouvrage « Guide pratique des 5S et du management visuel » mais ces 5 verbes d’actions peuvent aussi être traduits de diverses façons :
- Débarrasser / Ranger / Nettoyer / Standardiser / Progresser.
- Ordonner / Ranger / Dépoussiérer - Découvrir des anomalies / Rendre évident / Être rigoureux (soit l’acronyme « ORDRE »).
En revanche, l’ordre des actions est fondamental pour la méthode des 5S : on doit toujours commencer par se débarrasser de l’inutile avant de vouloir maintenir l’ordre et standardiser. Bien souvent, les 2 premières étapes sont les plus difficiles : savoir identifier puis se débarrasser des choses inutilisées depuis longtemps n’est pas toujours évident et requiert autant de méthodologie que de volonté.
La méthode 5S : enjeux et mise en œuvre
Les avantages de la méthode des 5S sont évidemment d’éviter le désordre, la perte de documents, la détérioration de matériel mais aussi d’éradiquer les accidents du travail dans le milieu industriel. En effet, un environnement de travail désordonné, peu ou pas entretenu, génère des pertes de temps sur des tâches sans aucune valeur ajoutée mais peut aussi causer des accidents. Le principal enjeu de la méthode est donc très clairement d’améliorer les conditions de travail au sens large.
Sa mise en œuvre est souvent insufflée par le service Qualité ou par un groupe de travail transverse qui sera chargé de son déploiement au sein des équipes, mais elle doit ensuite être portée, soutenue et suivie par la direction générale si l’on veut pérenniser la démarche. Concrètement, il faudra former les équipes à cette méthode et surtout, la déployer comme s’il s’agissait d’une politique interne dont chaque membre est « le gardien ».
Si la méthode des 5S est suivie méticuleusement, les bénéfices attendus seront nombreux :
- Augmentation de l’efficacité et de la productivité des équipes,
- Amélioration des conditions de travail et du bien-être de chacun,
- Réduction des gaspillages de temps et d’énergie à chercher un document ou un outil,
- Réduction des risques d’accidents du travail.
Existe-t-il des points de vigilance pour mettre en œuvre la méthode 5S ?
Comme souvent dans le cadre des méthodes d’amélioration continue, le succès des 5S repose beaucoup sur l’appropriation par les salariés ; cela doit devenir un réflexe de la part de chacun. L’écueil à surveiller lors de la mise en œuvre est alors « la rigueur militaire » : si la rigueur et l’ordre sont deux qualités caractéristiques de la culture japonaise, elles doivent être intégrées intelligemment dans les entreprises occidentales et différemment selon qu’on l’applique à un atelier de production ou à un bureau. Il semblerait en effet que les employés de bureaux et services administratifs sont moins enclins que les employés des ateliers à s’imposer un espace de travail « codifié ». La démarche 5S est donc moins une méthode qu’une bonne habitude à adopter au sein de l’entreprise afin de gagner en efficacité et en sérénité.
Exemples concrets de la méthode 5S en action
Afin de vous offrir une meilleure compréhension de cette méthode et de vous inspirer pour son utilisation dans vos processus de travail, explorons les différentes étapes en illustrant chacune avec des exemples concrets.
1 Seiri - Supprimer l'inutile
Dans un bureau, cela peut signifier trier les dossiers et documents stockés depuis des années. Supprimez les documents obsolètes de votre poste de travail, archivez ce qui est nécessaire mais peu utilisé, et recyclez ce qui est totalement inutile. De même, dans un atelier de production, vous pourriez éliminer les machines ou les équipements inutilisés depuis longtemps, libérant ainsi de l'espace précieux.
2 Seiton - Situer et ranger les choses
Dans un atelier, attribuez une place spécifique aux objets et aux outils, et assurez-vous que tout est étiqueté de manière claire. Dans un bureau, créez des systèmes de rangement logiques pour les fournitures de bureau et les outils, de sorte que tout le monde sache où trouver ce dont il a besoin.
3 Seiso - (faire) Scintiller et nettoyer
Dans un environnement de travail industriel, cela signifie maintenir les machines propres pour éviter l'accumulation de débris et de graisse dans leur zone. Dans un bureau, effectuez des tâches de nettoyage régulières pour maintenir la propreté des bureaux, des ordinateurs et des espaces communs et donc un environnement de travail sain.
Il n’est d’ailleurs pas inintéressant de croiser cet outil avec la méthode des 5P pour éradiquer les problèmes de propreté et de sécurité à long terme.
Voici un exemple de mise en application de la méthode des 5P, que vous pourriez retrouver dans le contexte industriel, et traiter à ce stade de la méthode des 5S.
Problème : un accident s'est produit à la suite du déversement d'huile provoqué par un dysfonctionnement de la machine de production.
- Pourquoi ? Parce que la machine a connu un dysfonctionnement.
- Solution : Réparer la machine de production.
- Pourquoi ? Parce que l'entretien de la machine était insuffisant.
- Solution : Établir un programme de maintenance préventive plus rigoureux pour s'assurer que les machines restent en bon état de fonctionnement.
- Pourquoi ? Parce que les ressources allouées à la maintenance préventive étaient limitées.
- Solution : Augmenter le budget alloué à la maintenance pour garantir un entretien adéquat.
- Pourquoi ? Parce que l'entreprise a réduit les dépenses pour la maintenance en faveur de la rentabilité à court terme.
Solution : Réviser la politique de réduction des coûts pour équilibrer la rentabilité à court terme avec la sécurité, en allouant suffisamment de ressources à la maintenance préventive.
Dans cet exemple, la méthode des 5P a conduit à l’identification de solutions qui seront utiles pour votre démarche d’amélioration continue.
4 Seiketsu - Standardiser les règles
Définissez des procédures de standardisation pour des tâches courantes. Par exemple, établissez des règles sur la manière de nommer et d’archiver des fichiers dans un bureau, ou créez des instructions claires sur la maintenance préventive des machines dans un atelier.
5 Shitsuke - Suivre et progresser
Dans un bureau, effectuez des audits réguliers pour vous assurer que les règles sont suivies, et encouragez les employés à signaler tout écart par rapport aux normes établies. Dans un atelier, surveillez la maintenance des machines, et organisez des sessions de formation pour le personnel sur les meilleures pratiques.
En suivant attentivement ces étapes, vous pourrez constater des améliorations significatives dans l’efficacité, la sécurité et le bien-être au travail. Les bénéfices se traduisent par une diminution des pertes de temps liées à la recherche de matériel, une réduction des accidents du travail, une amélioration de la productivité et une atmosphère de travail plus agréable pour tous les employés, quel que soit leur environnement professionnel. Vous évitez ainsi le concept de l’usine cachée, en exploitant toutes vos capacités sans aucune perte.
Vous l’avez compris : dans le cadre de l’approche Lean, la méthode 5S propose une approche simple pour améliorer l’organisation de l’espace de travail afin d’augmenter la productivité. Si vous êtes intéressé à explorer d’autres méthodes Lean, nous vous invitons maintenant à découvrir la méthode Kanban, qui facilite la mise en place d’une production en flux continu basée sur la demande.
Vous êtes dans une démarche d’amélioration continue ? Inspirez-vous des bonnes pratiques pour réussir la gestion de vos plans d’actions en téléchargeant notre Ebook :
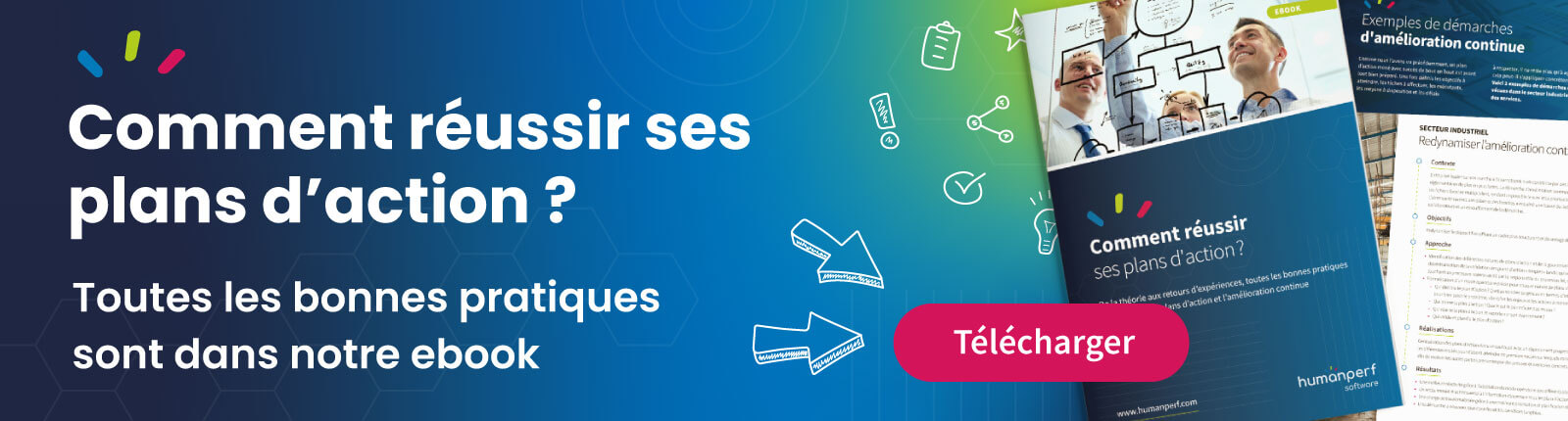
Cet article initialement publié le 18 avril 2019 a été mis à jour le 26 octobre 2023.