At the core of Lean Management, the 5S method is part of the ideal Quality toolbox to support the continuous improvement process in organisations. After being introduced by Toyota, this Japanese organisational practice is widespread in the world of manufacturing, but it can apply equally well to an office as to a workshop.
The objective to be achieved is straightforward enough: impose some order in the working environment and the equipment it contains to improve efficiency and safety.
The 5S method: definition
The starting point for the 5S method is the realisation that efficient, high quality work requires a clean, safe, properly run environment. The 5 letters ‘S’ therefore represent five actions to be taken in the workspace:
- Seiri: Sort to remove unnecessary items.
- Seiton: Set things in order, or Straighten.
- Seiso: Shine and clean, or sometimes Sweep.
- Seiketsu: Standardise the rules.
- Shitsuke: Sustain and progress, through Self-discipline.
Alternative translations of these five verbs are of course possible (some are given above). Henry Ford’s “CANDO” acronym is both a forerunner and a related idea, standing for Cleaning up, Arranging, Neatness, Discipline and Ongoing improvement.
The order of the 5S actions is vital. The process must always begin with removing unnecessary items before attempting to maintain order and standardise. The first two stages are very often the most difficult. Identifying and then removing items that have not been used for a long time is not always simple and requires both a will and a way.
The 5S method: aims and application
The advantages of the 5S method are, fairly obviously, avoiding untidiness and disorder, and preventing lost documents and damage to equipment, but the elimination of workplace accidents in industrial environments is a further benefit. A disorganised working environment, with poor or no maintenance, not only means time is wasted on tasks of no added value, but can also cause accidents. The main aim of the method is therefore clearly the improvement of working conditions in the broadest sense.
Application is often instigated by the Quality department or by a cross-functional working party which will be tasked with rolling the method out to employees, but it must then be driven, supported and monitored by senior management for lasting effect. In practical terms, employees need to be trained in the method and, crucially, the method needs to be rolled out in the same way as an in-house policy, of which each member of staff is the “enforcer”.
Thorough application of the 5S method brings a number of benefits:
- Improved efficiency and productivity from staff;
- Improved working conditions and individual welfare;
- Less time and energy wasted looking for documents or tools;
- Reduced risk of workplace accidents.
Are there any specific points to watch when implementing the 5S method?
As is often seen with continuous improvement techniques, the success of 5S is largely based on its acceptance by staff. It needs to become instinctive in all employees. One pitfall to guard against during implementation is “military discipline”. While discipline and order are two defining characteristics of Japanese culture, they must be applied intelligently in Western businesses, and tweaked depending on whether they are being applied to a shop floor or to offices. It would in fact appear that office workers and civil servants are less inclined than workshop staff to conform to a “regimented” workspace. The 5S approach is therefore less of a method than a set of good habits to instil into the business to boost efficiency and peace of mind.
If you are following a continuous improvement process, learn about best practice in delivering successful action plans by downloading our ebook:
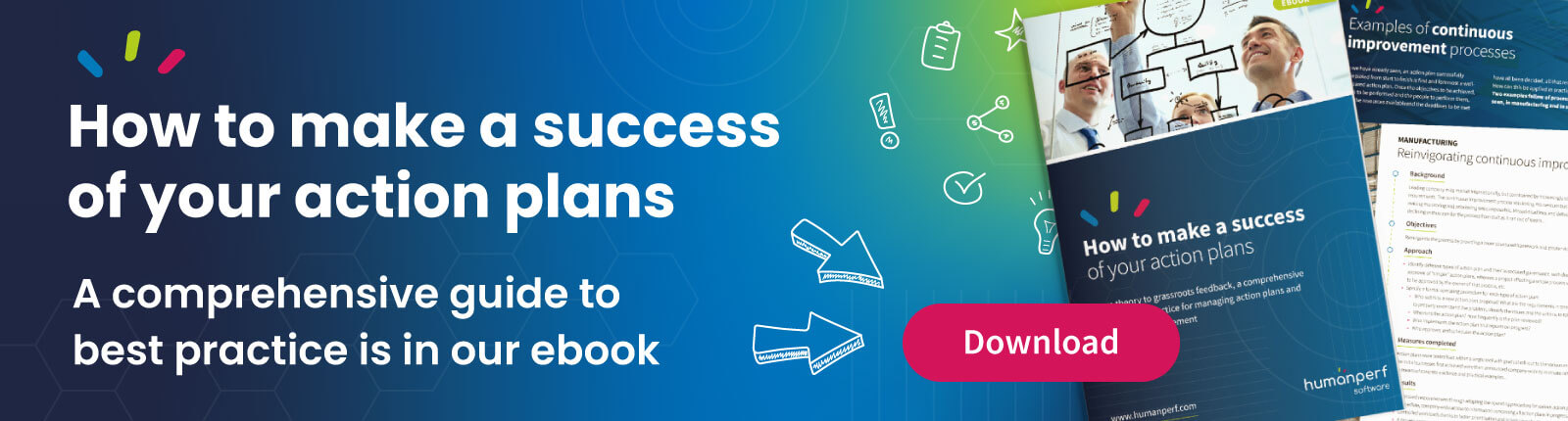