Derived from TPS (Toyota Production System) – Toyota’s innovative production system in Japan – the MUDA, MURI and MURA principles are at the core of the Lean Management philosophy. They play a crucial role in continuous improvement and optimization of organizational performance. These concepts focus on identifying and eliminating waste, variability, and overload in all production processes.
Their relevance extends far beyond manufacturing to office environments, service companies and public institutions, offering simple, cost-effective solutions to boost productivity and improve working conditions.
MUDA, MURA, MURI: Definitions
These three Japanese terms refer to the different types of waste to be avoided in a business environment to increase efficiency. The three key concepts play a crucial role in identifying the different types of waste to be eliminated in business processes, thus facilitating continuous improvement. Here are their definitions.
Minimize MUDA, towards efficient waste elimination
In Japanese, MUDA means waste, futility. Its concept highlights activities that use resources without adding value. Such waste generates additional costs, reduces efficiency and can compromise quality. The seven main categories of waste, grouped under the acronym TIMWOOD, include: Transportation, Inventory, Motion, Waiting, Overproduction, Overprocessing and Defects.
The aim of MUDA reduction is to optimize the use of resources, speed up processes and improve the overall quality of work.
Minimize MURA to reduce inconsistencies
In Japanese, MURA stands for irregularities and inconsistencies. This concept highlights the variabilities and inconsistencies in production or work processes, which can cause fluctuations in workload and affect quality.
These irregularities can lead to delays, overproduction or periods of inactivity, compromising overall efficiency.
The aim of MURA reduction is to standardize and harmonize operations to minimize these imbalances and optimize process fluidity.
Minimize MURI, or reduce overloading
In Japanese, MURI means overload, excess. Its concept refers to the overload applied to equipment or personnel, which can lead to errors, exhaustion and reduced efficiency. This overload can result from unrealistic expectations or poor planning, affecting the quality of employee performance and health.
The aim of MURI reduction is to create a balanced work environment that prevents overload and promotes sustainable productivity.
These three concepts together expose inefficiencies and offer a method for eliminating them, in order to achieve a smoother, more predictable workflow.
Identification and elimination of MUDA, MURA, MURI: Examples
MUDA reduction example (waste)
A manufacturing site identifies the unnecessary movement of materials between workstations as a major source of waste. By reorganizing the workspace to minimize these movements, efficiency is improved, and production time reduced.
MURA reduction example (irregularity)
In an office, irregular use of printers creates bottlenecks on some days and under-utilization on others. By analyzing printing needs and distributing tasks more evenly, irregularities are eliminated and resource utilization optimized.
MURI reduction example (overload)
In a distribution center, investment in assisted lifting equipment and the equitable distribution of physically demanding tasks reduces the overload on employees, improving their well-being and efficiency, while reducing the risk of errors and accidents.
These principles, though simple in theory, require a deep understanding of processes and a constant drive for improvement. By implementing them, companies can achieve significant gains in terms of efficiency, quality, and satisfaction for both customers and employees. Once the forms of waste have been identified, the 5S method – also created by Toyota – can be used to transform and improve the working environment.
Implementation of initiatives to capitalize on the MUDA, MURA, MURI identification process
The effective exploration and application of the principles of MUDA, MURA and MURI form a cornerstone in the pursuit of operational excellence within companies. The process begins by identifying the various forms of waste (MUDA), variability (MURA) and overload (MURI), paving the way for significant improvement. This recognition phase reveals optimization opportunities. Each opportunity must be analyzed, then followed up with initiatives to reduce or eliminate irritants.
Adopting these principles of continuous improvement requires deep integration into the company’s DNA, transforming vigilance and optimization into reflexes for all employees. However, adapting this rigorous discipline, rooted in Japanese culture, to the diverse environments of Western companies presents challenges. This adaptation must be sensitive to the specificities of each workplace, whether production workshops or offices, where the propensity to adopt a strict framework may vary.
The successful integration of MUDA, MURA and MURI depends on the organization’s ability to effectively drive performance while promoting a culture of change and continuous improvement. It’s crucial to avoid abrupt changes that may overload or demoralize employees. An evolutionary and collaborative approach is preferable, ensuring that every team member grasps and appreciates the value and benefits of these optimization methods.
To increase the effectiveness of these initiatives and ensure smooth management, tools like IDhall are a must. IDhall greatly facilitates the coordination, monitoring and analysis of improvement actions. This tool is essential for managing the action plans resulting from the identification of MUDAs, MURAs and MURIs, enabling organizations to maximize their performance potential.
Are you committed to continuous improvement? Get inspired by our best practices to successfully manage your action plans by downloading our Ebook:
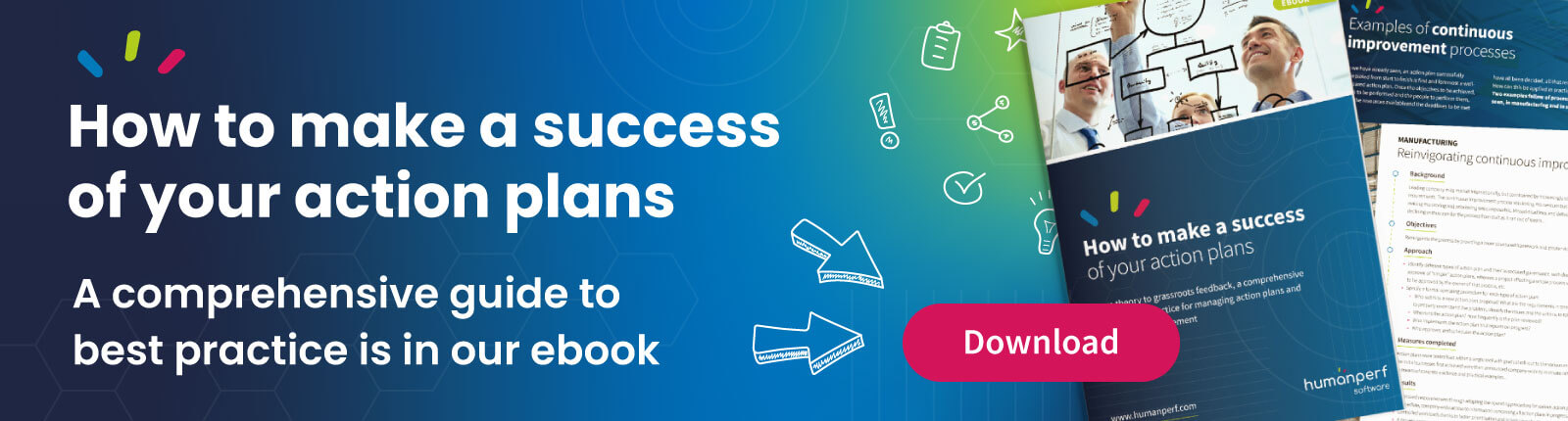