While change is one of the fundamental factors governing how the world works, it is nowadays synonymous with transformation and innovation for businesses, and seemingly essential to any modern development strategy. There are two ways to bring about change. One is to implement a one-off, radical, disruptive change; the other is to make incremental improvements, gradually, from day-to-day, which in the long run can take you even further in your change than you ever dreamed possible.
Kaizen, or the “art of continuous improvement through small steps”, fully embraces this philosophy of gradual change, where the existing system is the starting point for implementing “small” changes which are nonetheless able to make a real difference to performance and well-being in the workplace.
At a time when transformation and disruptive innovation are becoming the norm, potentially restricting employees’ room for manoeuvre, is Kaizen outdated? What are its limitations? Should it still be used?
Continuous improvement through small steps: the other way of considering issues
Improving quality of service, for example, is crucial for any business that wants to differentiate itself to its customers, but it is first and foremost essentially an ongoing mission; it is a journey not a destination.
As part of continuous improvement, Kaizen consequently makes it possible to develop and improve working processes by implementing changes regularly. Such changes might relate to production methods, corporate culture or security, but they will always be small, practical measures that are straightforward, inexpensive and can be applied quickly. Kaizen is a state of mind, whereby all members of staff make an effort day-to-day with a view to “always do better”, over the long term.
The Kaizen philosophy was developed in Japan. Kaizen is a concatenation of “kai” and “zen” meaning “change” and “better” respectively. The approach is intended to move towards perfection across all processes, albeit without needing to revolutionise the entire way of doing things.
To drive perpetually forward, there are four mainstays to Kaizen:
- Reject dogmatic stances and challenge preconceptions;
- Take as much interest in the approach and the process as the final outcome;
- Work within a global framework to provide an overview;
- Do not judge or blame, to avoid discouraging employees.
One of the key aspects of Kaizen is to reduce waste, “muda” in Japanese, of which there are 7 types:
- Over-production,
- Stocks,
- Waiting times,
- Transport,
- Defects,
- Motion,
- Over-processing.
Adopting a Kaizen approach generally makes it possible to reduce processing times for all services and optimise productivity while improving employees’ working conditions. In contrast, Kaizen is a proactive process, not a reactive one. It targets continuous improvement, not problem resolution. Kaizen consequently happily runs alongside other continuous improvement processes such as the DMAIC method, Lean management and Kanban.
When should Kaizen be used in a business?
Kaizen is a philosophy that can be adapted to suit any type of organisation, but is more useful in those that have full control over their operating environment and existing work processes; in organisations that are not so much looking for disruptive innovation to “change everything at all costs” as for continuous improvement to existing processes. Kaizen is thus a perfect fit for large companies and highly process-driven industries.
The three fundamental aspects to successful deployment of Kaizen within a business are:
- Expertise: technical skills and skills requirements;
- Interpersonal skills: namely the ability to listen, understand, analyse and take into account;
- Imparting knowledge: the ability to communicate and convey information.
Before embarking on such a procedure, it is vital to ensure that the corporate culture matches this philosophy. Successful implementation of Kaizen presupposes that all employees have the chance to be heard, which itself requires management’s active involvement.
Continuous improvement through Kaizen and participative innovation: a marriage of convenience?
Kaizen is a way of “working better together” whereby each member of staff has a voice, so to speak. As a result, it is similar to a participative innovation process where everyone can freely express themselves at any time, suggesting ideas to improve their working environment.
The company must therefore encourage employees to suggest their ideas, assuring them that they will be listened to. Without ideas, Kaizen simply stalls. It is therefore essential to arrange beforehand to collect ideas as simply and efficiently as possible. However, the traditional “suggestion box” ceased to be suitable a long time ago, and it is important to now invest in a modern, digital, collaborative innovation platform that enables all concerned to contribute to the Kaizen process simply and intuitively.
To incorporate Kaizen within your continuous improvement process, feel free to download our ebook and follow its good advice to ensure all your action plans are successful:
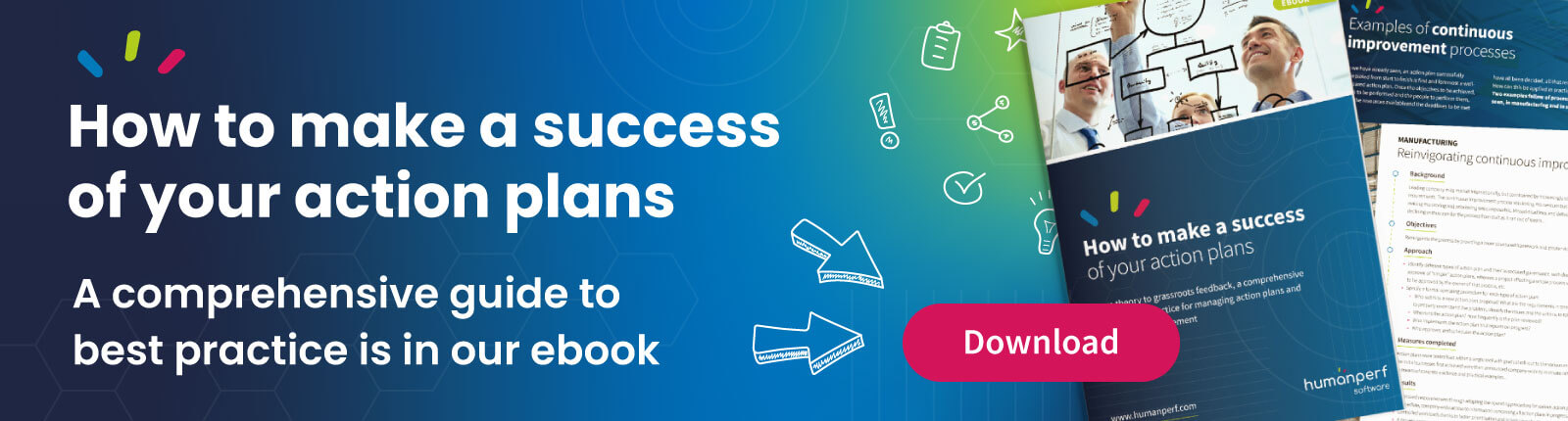