The DMAIC method is well known to those professionally involved with operational excellence and continuous improvement. It is first and foremost a common-sense approach for daily use when running projects to find lasting and permanent solutions to problems whatever form they take, e.g. reducing irritants, eliminating non-compliance, improving the customer experience, etc.
The DMAIC method
The DMAIC method is a scientific problem resolution method divided into five phases giving rise to the abbreviation, namely Define / Measure / Analyse / Improve / Control.
A summary of the five DMAIC phases:
- Define: To set out the problem by determining its symptoms.
- Measure: To quantify the scale or size of the problem.
- Analyse: To determine the cause(s) of the problem.
- Improve: To identify the solution(s) to the problem.
- Control: To check and maintain the improvement over time.
The DMAIC method fits flawlessly into a continuous improvement process such as a Deming Wheel (or the Plan-Do-Check-Act method - PDCA). The only difference from the PDCA method is that DMAIC is an actual component of Lean Six Sigma projects.
The origins of the DMAIC method: Lean Six Sigma
Lean Six Sigma is an approach based on collaborative team effort to improve processes, and therefore performance, in an organisation while eliminating waste. “Performance” in Lean Six Sigma refers not only to productivity but also improvements in quality, lead times or costs.
The Six Sigma method was invented at Motorola in 1986 as part of a search for customer satisfaction by optimising manufacturing processes for greater quality and efficiency. Initially limited to manufacturing processes, the method then spread to all types of processes (administration, logistics, sales, etc.).
DMAIC is a powerful technique and a logical consequence of Lean Six Sigma. To achieve customer satisfaction objectives, resource savings, environmental protection or indeed improved working conditions, the problems encountered must first be understood then resolved. Which is where DMAIC comes in, by analysing the problem to be fixed in detail and identifying the most effective solution.
You might actually have been using DMAIC for years without realising it.
Using the DMAIC method
To apply the method properly, and gain the best from it, it is advisable to involve all project stakeholders, including senior management, in all five phases.
1Define
The first stage in all DMAIC projects is to produce the “Project Charter”, which describes the problem encountered, the people or customers involved, key indicators and the objectives to be reached, the scope, schedule and project team, not overlooking the expected benefits of the project. The 5W1H method can also be used to provide answers to some aspects.
2Measure
This phase entails determining the relevant measurements or metrics to collect to fully understand the baseline process and the scale of the problem to be resolved.
3Analyse
The data collected following the previous phase can then be examined and dissected to analyse the process at issue and determine the cause(s) of the problem.
4Improve
Once the cause(s) of the problem have been identified, it is time to consider possible solutions. There may be a number of possibilities, and it is advisable to sift through them to select the solution(s) to implement to achieve the desired objectives.
5Control
This entails continuous improvement and operational excellence, so it is crucial to set up an action plan management and monitoring program for those solutions actually implemented, making it possible to measure the degree of improvements achieved and their longevity.
Looking beyond method to governance of DMAIC projects
The key feature of DMAIC projects is that they are based on tried and tested organisational methods structured around the different Six Sigma certification levels (White Belt, Yellow Belt, Green Belt, Black Belt and Master Black Belt) that are awarded to individuals after taking various training courses and running different projects.
Although DMAIC is a very common sense approach, it does not merely happen by management decree. Training is a vital component of the process, so as to:
- Understand the philosophy and issues;
- Gain proficiency in tools and systems;
- Coordinate a project, a project portfolio, and the associated resources;
- Promote operational excellence.
As Antoine de Saint-Exupéry said, “A goal without a plan is just a wish,” so the structured aspect to the DMAIC method may therefore be of invaluable help in some of your projects. To find out about best practice in delivering successful action plans, download our ebook without delay:
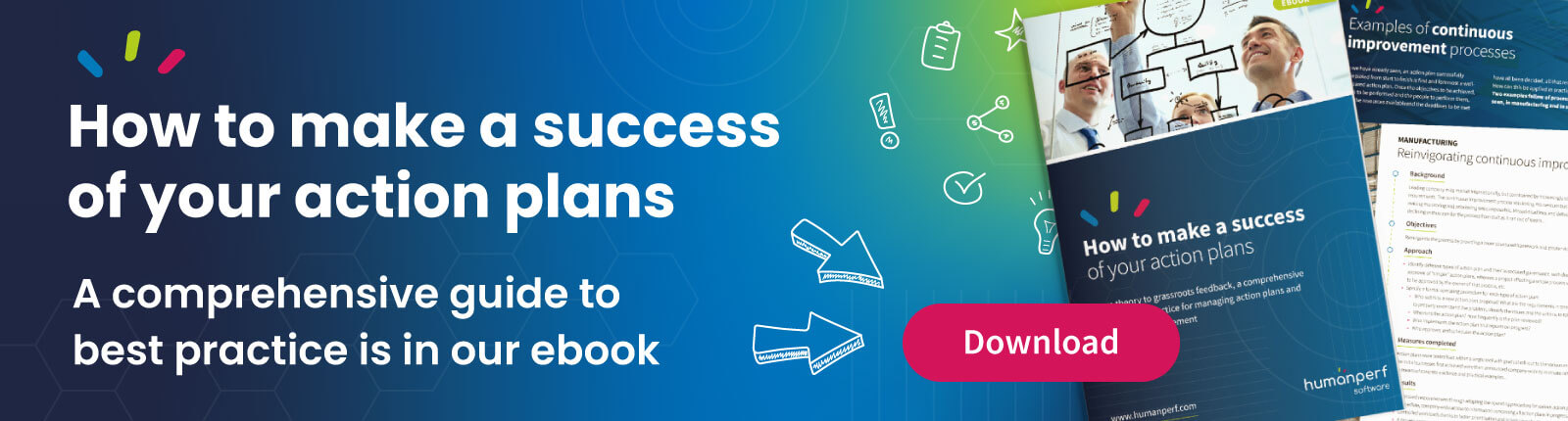