Perpetually seeking, and actually making, progress is highly desirable, even vital, in any modern business. All employees must be able to work as effectively as possible, achieving the best possible level of quality.
The PDCA (Plan, Do, Check, Act) method, also known as the Deming Wheel, is the ideal response to this need. The spearhead of continuous improvement for many years, this famous concept, first developed in the 1930s, is one of the cornerstones of performance improvement thanks to its simplicity, universal applicability and flexibility.
Defining the PDCA method
Physicist and teacher Walter Andrew Shewhart developed this management and quality control method in the 1930s. His theory was then refined by the statistician William Edwards Deming, whose key contribution was to add a visual dimension, and then introduce it to Japanese manufacturers in the Nippon Keidanren federation in the 1950s. The PDCA method is now therefore closely linked to his name, referred to as the Deming Wheel.
PDCA nonetheless remains a mnemonic for remembering the steps to be followed to improve performance and quality in an organisation:
1P for Plan: or prepare, schedule
This step is used to take stock of the situation and pinpoint the real problem, and then build the appropriate action plan and determine the KPIs that will subsequently serve to measure the success of those actions.
2D for Do: or carry out, implement
This step is where the action plan is carried out, ensuring all stakeholders are properly informed of the schedule of operations.
3C for Check: or inspect, verify
Here is where the organisation starts to measure results, using the KPIs. If the objective is not achieved, it is advisable to take the remedial measures required, and to seek out the root causes, which perhaps were not sufficiently well-identified at the outset.
4A for Act: or adjust, amend
The post-implementation review stage: is the matter closed, or does the cycle need to be restarted? When the objective is met, that is when best practice becomes standard practice for the future.
Turning the Deming Wheel
This 4-step cycle establishes a virtuous circle that the Deming wheel highlights perfectly. Each ratified idea is converted into action, each completed action becomes knowledge and so on and so forth. Progression and improvement are continuous, which is why the Deming Wheel is often represented in graphics supported by a chock or wedge: the wheel only rolls in one direction and achievement is always made secure.
While the PDCA method appears very straightforward, its implementation demands both thoroughness and discipline if it is to be most effective. In practical terms, precise and measurable objectives need to be set, based on the observed reality at the grassroots of the organisation. Clear communication about the planned action must be ensured. The PDCA cycle supports action while objectives are still not yet met. While the method can be used to treat the symptoms of malfunction, its main purpose is to cure the root cause of problems.
It is then crucial to make the wheel turn, and the onus for that is on management! The potency of the PDCA method lies in how it enhances action plans with every rotation of the wheel, and improves the overall performance accruing to the business. Progress should be regular with no skipping steps and no sticking on one step indefinitely. The experience accumulated over time will make it possible to implement ever more lasting and appropriate solutions.
Practical uses of the PDCA method
Of all continuous improvement systems, the PDCA method is very useful for identifying failings or shortcomings and then eradicating problems. The world’s best-performing businesses, already very experienced in Lean Management, often make it their main instrument for implementing, checking, and then standardising best quality practices.
Now used in HR, marketing, finance and logistics, among others, the method has left the factory floor and spread everywhere it can be of use. Which is exactly what is great about it - it can be applied to any issue. Because it supports action while objectives remain unmet, it is as effective in an office as it is in a manufacturing plant.
The Deming Wheel enables learning and performance improvement to thus become constant features within an organisation. It remains as relevant as it ever was in the modern world where economic and social environments are increasingly difficult to fully understand. Start-ups, where agility is the key word, have grasped this and have also adopted the technique in their working methods.
To find out about best practice in delivering successful action plans, download our ebook without delay:
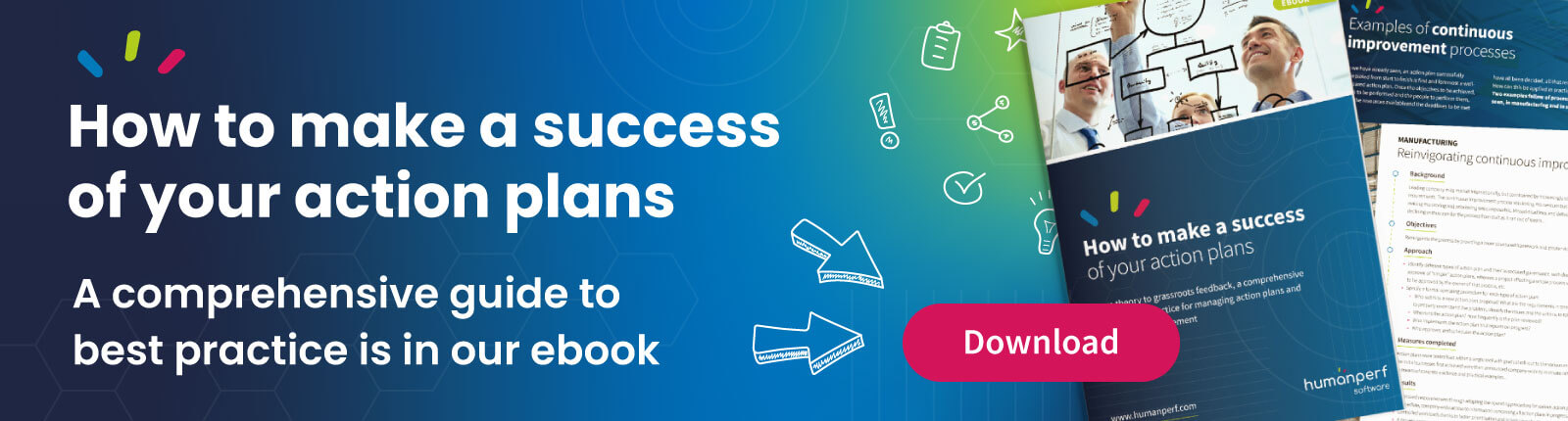