Lean management can be summed up as the idea of bringing ever greater value to customers by eliminating activities that add none. Be careful, though. Lean management is not a magic wand; it is a structured approach that can drive significant development within a business. The following shows why and how…
The customer is the most important part of the production line.
Lean management in brief
“Lean” is the adjective bestowed on the methodology created by Toyota in Japan in the 1970s, within its plants. At the time, it could be defined as management without waste. Although it was initially deployed in the automotive industry, lean management is a philosophy that can, of course, be applied to all types of organisation and any number of business sectors.
The primary aim is performance gains through continuous improvement to satisfy customers by improving productivity, quality, lead times and costs. The four cornerstones of lean management are teamwork, communication, efficient use of resources, and the elimination of waste.
Much more than a mere method, lean management entails systematically working towards the active resolution of production problems at various levels of a company:
- Elimination of over-production
- Stock reduction
- Shorter lead times
- Cost control
- Transport optimisation
- Skills maximisation
- Communication optimisation
- Improved quality
In summary, lean management makes it possible to provide highly-skilled work in ideal operating conditions using the least possible time, resources and energy. It aims to bring greater value to customers by removing activities of no value.
Where to start with lean management?
While a great deal is heard about lean management, and it can be implemented essentially anywhere, it is not always obvious how to adapt the method to a given context. The principles are straightforward enough and the benefits are clear, but where to start?
Changing mindsets is one crucial initial step. Conventional methods no longer work, and a paradigm shift is vital because the wealth of a business is first and foremost the knowledge and expertise that exist across the entire organisation, from senior management to the shop floor.
Once the mindset is right, it is important to properly understand that even if lean management is connected to many effective techniques, such as Lean Six Sigma and the DMAIC method, Kaizen, the 5S method and Kanban to name but a few, it is much more than just another method, and is more akin to a philosophy. It is therefore advisable to approach it by taking the following four vital steps:
- Identify the company’s business requirements.
- Identify the potential for operational improvement.
- Evaluate the capacity for change.
- Produce the action plan.
1Identify the company’s business requirements
This phase entails understanding what it is that generates the value of the product or service offered, its positioning relative to competitors, its customer promise. From this point, requirements as regards improvements in terms of quality, costs and lead times can be analysed. It is important at this stage not to overlook external constraints that could influence the actions taken.
2Identify the potential for operational improvement
Besides business requirements, the potential for operational improvement needs to be understood. This is where the organisation identifies any waste of resources at grassroots, by analysing various operational metrics: service level, team efficiency, production process lead times, etc. The various potential gains must be quantified if they are to be converted into measurable objectives. The “Gemba walk” (taken from the Japanese word “genba” meaning the real place) is particularly well suited to this phase because it consists of a purposeful walk around a workplace to conduct an audit and become aware of what is actually happening with operational staff at the coalface of value creation.
3Evaluate the capacity for change
Once the need and potential for improvement have been identified, the next step is to understand how it should be brought about. What is the organisation’s capacity for change? How much time should be anticipated to implement these improvements? What brakes and accelerators are found in the organisation? Just some of the questions to be answered before starting the last phase.
4Produce the action plan
For transformation to succeed over the long-term, it requires operational action plans. The key to success is to address continuous improvement in a structured, systematic and consistent manner.
In addition, if you want to find out about best practice in delivering successful action plans, download our ebook without delay:
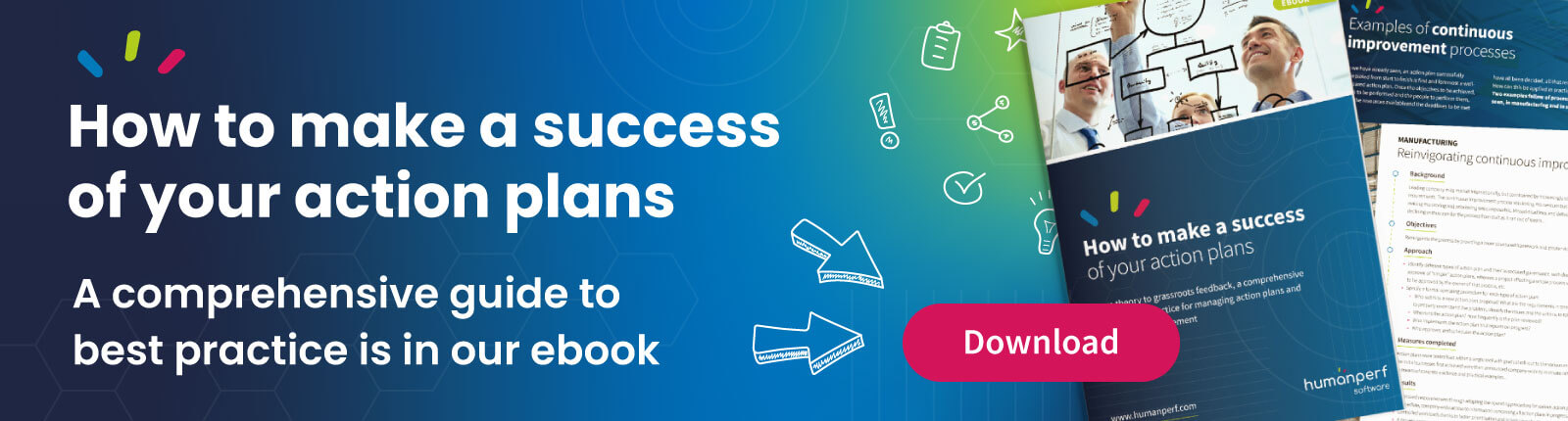
The real benefits of lean management
It is a tried and tested method in constant use since it was devised in the 1970s. Promoted by the major consultancy firms, who sang its praises in terms of potential for increased productivity, it consistently delivers four main benefits:
- It institutes a durable process: lean management is for the long-term view, not for finding quick fixes for short-term profitability.
- It encourages stable organisation in the company: lean management creates de facto loyalty in customers and employees, as both are at the heart of value creation in the business.
- It combats waste effectively and does so at all levels (manufacturing, management, sales).
- It facilitates business digitisation: by highlighting tasks of little added value, line management duplication, and improved customer/supplier/employee relations, lean management is a natural driver for paperless procedures and widespread automation.
How does lean management differ from other continuous improvement techniques?
Lean management helps with “working better together”. A “Lean Manager” not only tries to find ways and means for staff to improve, but also tries to understand, with employees, what “working better” actually means in their specific context.
Lean management therefore makes possible long-term, profitable improvements in the organisation’s processes, which is how it keeps all its continuous improvement promises.
In the same way as other quality methods, lean management has ultimately become something of a cliché. However, used properly, i.e. making customers and employees the top priorities, it remains one of the most potent techniques for lasting growth that genuinely creates value.
To find out more, now read our article on successful management of the continuous improvement process.
