Against a backdrop of profound transformations to our ecosystem, putting significant changes in place within an organisation gradually, instead of sudden internal or external upheavals (change in management, market instability, etc.) would appear to be common sense. Importantly, doing so is also a genuine strategy based on a long-term view and day-to-day implementation of change at grassroots.
This is a climate in which operational excellence makes perfect sense, in terms of creating and then maintaining perfect equilibrium between a strategy and its execution by people, processes and technology. The outcome is that this equilibrium generates a rewarding employee experience and a satisfying customer experience, and both of these outcomes are sources of excellence for the business.
However, while switching from performance to excellence is the stuff of senior management’s dreams, how is it achieved?
What do we mean by operational excellence?
In the old millennium, continuous improvement and operational excellence could refer to the same thing, while innovation remained the exclusive preserve of the R&D Department. Since then, competitive pressure and unstable economic environments have demanded that we rethink our businesses in the round, in order to offer differentiating aspects at every level.
To explain more fully, let’s review the three key principles of operational excellence:
1Customer focus
A company’s added value is only that which is perceived as added value by customers. This requires attention to be paid to customers so as to adjust products and services to match their actual requirements. Operational excellence consequently provides an answer to the question “how can products and services be designed to perfectly meet customers’ needs?”
2Efficiency
Over and above supplying the right product or providing the right service, it is also important that an organisation does so efficiently, i.e. by eliminating waste and optimising efficiency along the entire value chain. Here, operational excellence answers the question “how can better, faster and cheaper production be achieved?”
3Engagement
The most effective results will be obtained by encouraging perpetual improvements to the process from all employees and boosting their capacity for self-organisation. Operational excellence for this aspect answers the question “how can lasting engagement be secured at all levels from senior management to operational staff?”
So, is it a philosophy or a process?
This is a genuine question and there is no guarantee that there is only one answer. Far from being a mere method, operational excellence is first and foremost a change of mindset within the organisation itself. We can then talk in terms of a philosophy, where customer requirements, application and self-assessment are all to the fore. Operational excellence is absolutely not a cost-cutting approach; lower costs are simply an effect brought about by the constant search for improved efficiency over the long term.
Nor is operational excellence an idealised and intangible view of business reality. Any business, in seeking operational excellence, must have a business-oriented view and quantified targets, because the process requires a high level of investment over time from all members of staff.
Operational excellence is perhaps both things at once, because nowadays it has a wider and more open scope, leaving more room for (re)designing processes, integrating new technologies and broadening the company’s offering to create more value.
Continuous improvement or innovation? Is operational excellence the Holy Grail?
These two aspects can no longer be ignored and dealt with separately, otherwise there is the risk the business will ultimately face some substantial contradictions. Operational excellence obviously shares a great deal of common ground with continuous improvement, such as problem resolution and waste reduction. And these are issues for which methods such as Lean, Six Sigma, 5S and Kaizen can clearly deliver some appealing answers.
To find out all about best practice for delivering successful continuous improvement processes, download our ebook without delay:
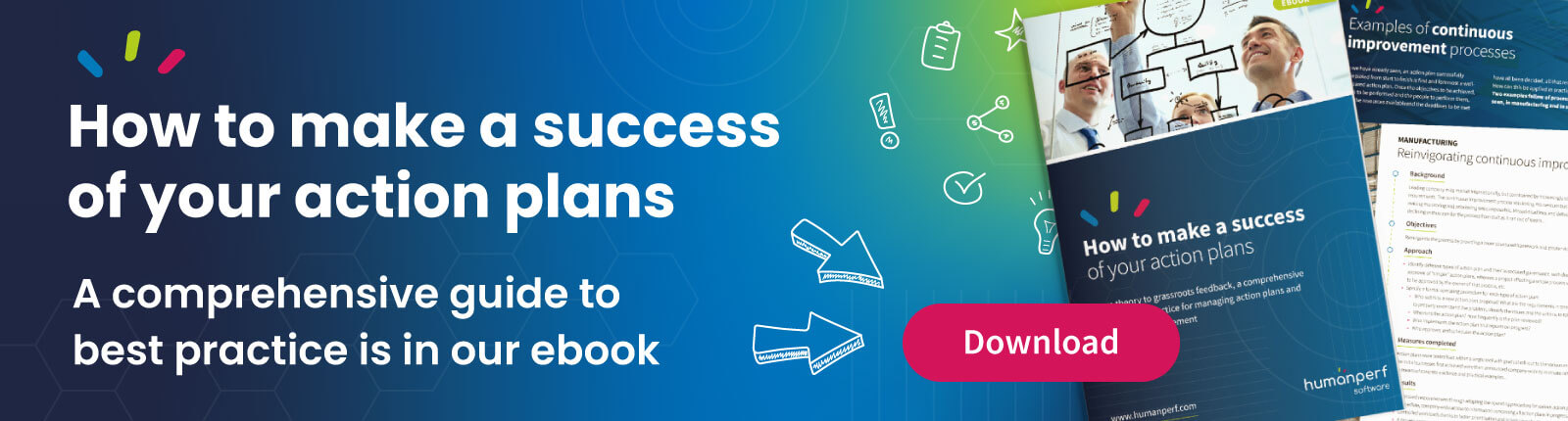
However, the new dimension brought by operational excellence is the greater extent to which it seeks to ensure that continuous improvement and innovation are perfectly aligned with the business strategy, and fully integrated into corporate culture. This perpetual quest for perfection must be demonstrated as a matter of routine in all aspects of the organisation, addressing four main areas.
Satisfying customers
Customers are at the core of operational excellence, and drive it forward. This does require the right viewpoint, i.e. that the only real value is the value perceived by customers. It means that R&D teams sometimes have to leave their comfort zone by, for example, considering co-creation of products or service enhancements with contributions from customers.
Ensuring all employees share the same vision
Employees’ day-to-day engagement needs them to share the same view of the business, which itself requires constant communication from senior management and line managers, explaining a) the objectives and b) the resources made available to all staff in order to achieve them.
Putting people first
Respect for each individual and his or her ability to contribute to value creation is one of the leading principles of operational excellence. All businesses must ensure they are able to listen to and accept suggestions made by all and any stakeholders. Improving recognition and trust is a clear route to improving the involvement and productivity of all employees.
Galvanising all stakeholders, inside and outside the business
Each function and every department in a business is connected, including sometimes to external entities, when we consider the “extended enterprise” viewpoint. It is therefore important to have a broad picture of the organisation and to ensure that information and good ideas circulate around it. This will result in all concerned taking responsibility and making better decisions.

Operational excellence in R&D at SWM International
Good performance in a global manufacturing outfit is unlikely to be achieved if the R&D is compartmentalised and spreadsheets are used to track R&D projects. Therefore in 2015, SWM International decided to overhaul its R&D organisation to improve time-to-market by adding a department-wide team and implementing IDhall. Read the R&D team’s testimonial on successfully cutting average project durations to a third or quarter of their previous length.
Operational excellence or flawless alignment between a business’ strategy and culture
In some businesses, the search for operational excellence is more a matter of following best practice and other continuous improvement methods. In these situations, it is not embraced by senior or line management, and even less so by employees as a whole. Continuous improvement, innovation and transformation remain compartmentalised processes, and no output from them can lay any claim to excellence.
On the contrary – operational excellence must truly form part of the company’s DNA, and be “inherited” by all staff, from employees who accept it with an open mind into their daily routine, to managers able to lead their teams with humility and goodwill.
Individual attitudes are the factor here, which only corporate culture can change. Operational excellence is therefore less a question of methods and systems than a corporate strategy focused on securing employee buy-in to the long-term view, appropriately and impeccably implemented at all hierarchical levels of the organisation.
While operational excellence makes it possible to run faster, decision-making excellence serves to first make sure we are running in the right direction. Collective intelligence can in fact help to reduce decision-making risk connected to highly challenging issues, in particular anything affecting the business collectively or relating to complex matters, but how can it be applied in practice?
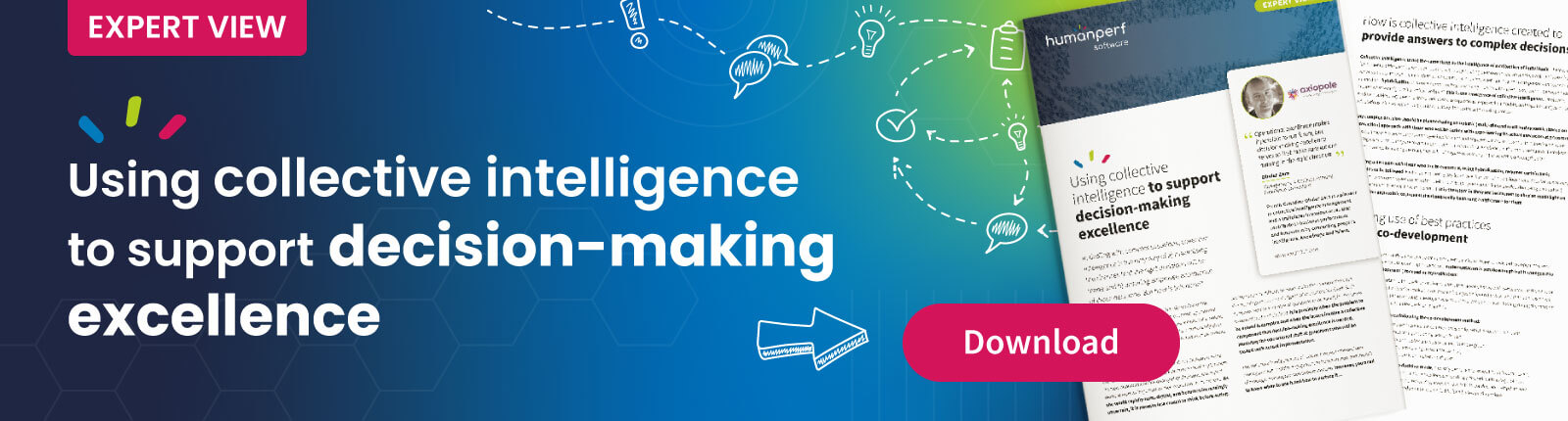