Of the numerous quality techniques and problem resolution methods available, the 8Ds method (also called 8 Dos or 8 Disciplines) seems the most comprehensive. It requires a thorough procedure to be followed to eradicate the causes of non-quality. It has twin objectives, namely swift response to a problem and the long-term removal of root causes.
Originally, this continuous improvement process emerged from a military technique used by the Americans during the Second World War. However, it was the Ford Motor Company that brought it back into favour in around 1987.
The 8D method objectives and framework
The 8D method is a quality procedure the aim of which is to eradicate problems within an organisation. It is based on the experience of those affected by the problem, and is effective because it is collaborative. It can also be used to deal with inter-process and inter-departmental problems, and indeed issues with customer or supplier relationships.
The objective of the 8D method is to offer a systematic approach to problem resolution through cross-functional, multi-disciplinary teamwork. In so doing, it boosts continuous improvement and delivers lasting solutions to irregular problems.
The 8D method consequently provides a standard framework through a formal process for handling unexpected problems which ensures systematic investigation to determine root causes and elimination of those problems such that they never occur again. The resulting solutions are continuously improved and used as templates to capitalise on the lessons learned.
What are the 8 activities in the 8D method?
As its name clearly indicates, the 8D method is based on 8 steps, to be followed to the letter, one after the other, without skipping any.
1DPlan the 8D process
- Set up a team with the skills, time and authority necessary to resolve the problem.
- Designate a leader and spokesperson within the team.
- Clarify objectives and responsibilities.
- Present the methodology.
2DDescribe the problem
- Use the 5W1H method to specify the problem.
- State the issues.
- Identify any constraints.
3DIdentify and implement interim actions
- Define remedial measures (to fix the problem short-term without, at this stage, addressing the root causes).
- Implement these containment measures.
- Measure the effectiveness of the action plan.
- Use this step to deepen understanding of the problem.
4DIdentify the root causes
- Identify all the potential causes of the problem (using brainstorming, the 5 Whys method, or Ishikawa (cause and effect) diagrams).
- Check each cause by testing, or against any available data.
- Identify all assignable causes.
- Determine alternative corrective actions to the interim measures taken, to eliminate the real causes.
5DApprove and implement permanent corrective actions
- Organise the team’s work on the basis of the skills required.
- Confirm that the corrective action selected does actually resolve the problem (supported by tests and experience).
- Determine the solution validation criteria (cost, material or human resources, lead time, impact, etc.).
- Schedule implementation of the actions.
- Organise monitoring of the action implementation.
- Track future developments.
6DMeasure the effectiveness of permanent corrective actions
- Evaluate the outcomes through tests, feedback or audits.
- If the objectives have not been reached, re-convene the 8D team to analyse the reasons for failure and undertake the new actions required.
7DPrevent recurrence by standardising improvement actions
- Identify any possibilities of the problem recurring in future.
- Specify preventive control measures and metrics and indicators to confirm effectiveness.
- Update internal documentation (procedures, instructions, operating guides, organisational charts, etc.).
8DCongratulate the team
- Thank the personnel involved for their contribution and collective efforts.
- Recognise the work done and time spent by the participants.
- Identify the lessons learned during the project (the positive outcomes and difficulties encountered alike).
- In-house announcements can encourage use of the method and motivate employees.
The 8D method summed up
The 8D method often culminates in an 8D Report, a single document summarising the 8 steps taken. Many examples can be found online.
In summary, it should be kept in mind that the 8D method is thorough and applies perfectly well to complex problems. It is first and foremost a collaborative procedure, in which no step can be omitted. Nor should participants take the easy route of opting for “obvious” causes.
Lastly, measurement of the effectiveness of outcomes is vital to ensure their long-term success and that a problem has been permanently eradicated.
To find out about best practice in delivering successful action plans, download our ebook without delay:
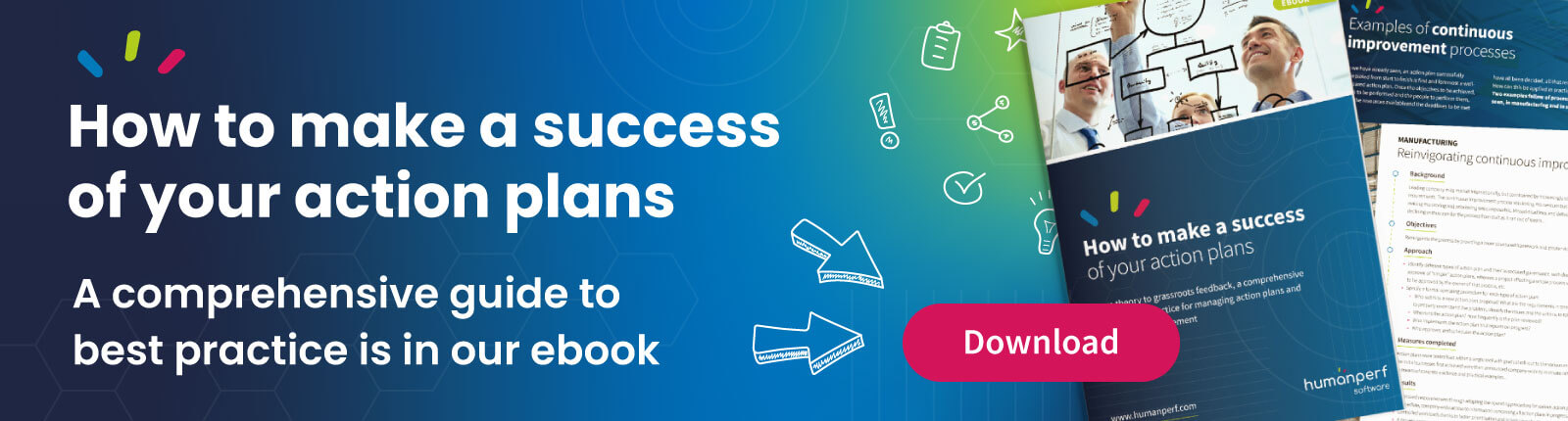