With the rise in small-scale production customised to individual customers, increasingly varied product innovations and ranges, marketing creativity and the multiplication of packaging, and so on, despite all the efforts made in terms of continuous improvement and Lean Management, for a long time now energy has tended to be scattered around the manufacturing sector, sometimes at the risk of losing full control over certain hidden costs, which could weigh heavily in the balance.
The concept of the “Hidden Factory” is consequently increasingly mentioned, a parallel universe often unknown to senior management where all kinds of shortcomings, delays, waste, duplicated effort and other workarounds of processes that are unsuited to reality on the factory floor are to be found. These same senior managers might be investigating new areas for investment in production capacity or storage facilities when they should first be checking that sufficient resources are being applied to the costs of non-quality. Because ultimately, the equation is a simple one: lower pointless expenditure = higher profitability and better competitiveness.
The definition of the hidden factory concept
The concept of the hidden factory describes unused capacity in a factory, or more broadly in any business. While the term has its roots in manufacturing, the concept can now be applied to any kind of business. And what is this unused value-creation capacity?
It could be defined as the maximum amount of additional output that could easily be generated with no additional capital expenditure. For the manufacturing sector, this would mean having production capacity running at almost 100% across all potentially useable time slots with a nonconformity rate of close to zero. More broadly, it means all the value that could be created if energy, material and human resources were not wasted pointlessly and without management’s knowledge.
The term hidden factory was popularised by the American statistician Armand Vallin Feigenbaum in the late 1970s. Feigenbaum described this hidden factory within his concept of Total Quality Control (TQC), targeting in particular waste and costs caused by “poor work methods” a large part of which are hidden below the surface of day-to-day operations. He believed that up to 30% of a factory’s activity was unplanned and was therefore, in a way, unused.
The hidden factory thus equates to all the energy spent on activities that create no value and that unfortunately remain invisible, as they feature in no report and are described in no procedure document.
Uncovering your hidden factory
All too often, when a product defect is detected, a work-around solution is found, meaning it is taken off the production line for correction, then put back on the line. While this resolves the problem for the short term, the process quickly departs from its ideal model if the same step is taken repeatedly, and the resulting variation then produces non-quality. Welcome to your hidden factory!
Unfortunately, a hidden factory is rarely the result of a single problem within one process, otherwise it would be easy to fix. It is typically the result of an accumulation of a number of non-quality problems at different stages in processes which, for want of being dealt with under a well-organised continuous improvement procedure, have seen by-pass and workaround solutions become, over the course of time, par for the course. Old hands explain to new starters what has to be done without necessarily remembering the original cause of the problem. A situation reminiscent of the five monkeys theory, or the story of social conditioning.
A very large number of factories, and businesses more broadly, fail to take into consideration the non-quality generated at every stage of the process when calculating their quality rates. This is why Amand Feigenbaum underlined the concept of total quality level which calculates the rate of return at each step and thereby highlights the “rework” necessary and the size of the hidden factory.
It is therefore vital to systematically seek out non-quality at every step, and this applies just as much to, say, a management control procedure as it does to production quality methods. The objective is to hunt down waste! A number of approaches can be used to do so, such as the 5Whys method, the 5W1H method, and the 8D or 8 Do steps.
To find out all about best practice for delivering successful continuous improvement processes, download our ebook:
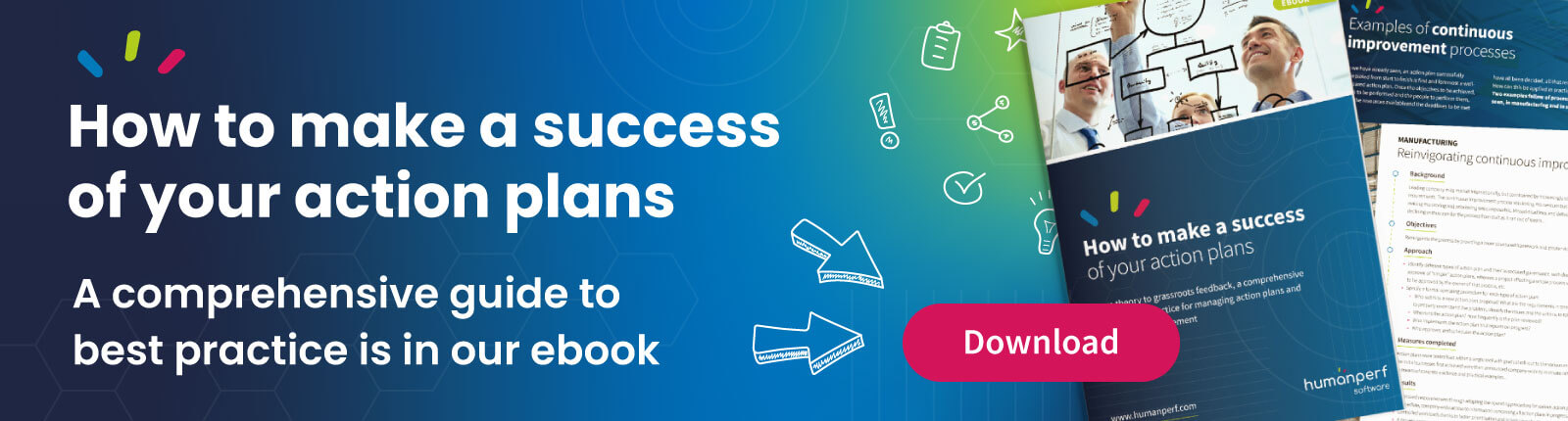
The hidden factory’s potential
The hidden factory is not always a myth, and many a production manager has been surprised to discover that actual output capacity is far higher than they thought. By reducing or even eliminating the costs of non-quality, more and better production, and indeed increased sales, can be the result. Feigenbaum reckoned the costs associated with hidden factories could adversely affect revenue by up to 25%.
This also invites us to consider the development of Industry 4.0, with smart, connected and robotised production plants offering genuine opportunities to businesses, but where the range of different technologies used absolutely must not bring about any expansion in hidden factories.
To guard against this risk, it is crucial to keep in mind the importance of experiencing the issues and not merely observing them. Having a precise picture of business performance reported by those running day-to-day operations is essential to prevent hidden factories developing. This links back to the subject of our last expert view: when dealing with complex situations, decisions taken behind closed doors, at the top of the management pyramid, are not always appropriate to the reality at grassroots. This being so, how can the decision-making process be adapted to boost the role of collective intelligence?
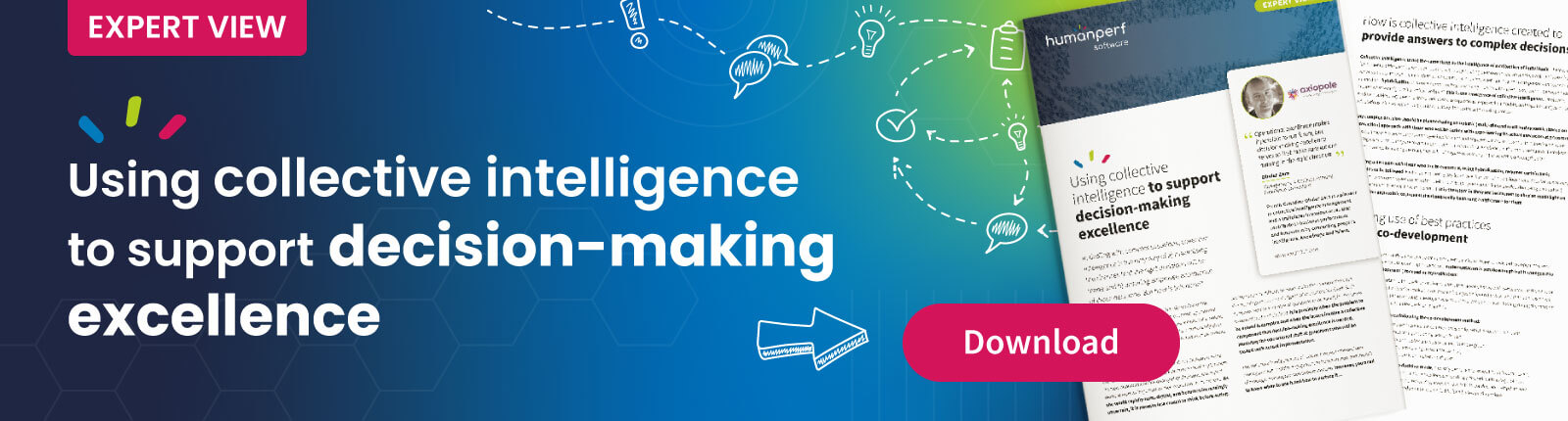