VMS, or Value Stream Mapping, is a technique used to visually represent all the stages within a work process, or value chain. Formalising all the jobs, and the circulation of information flows, within an organisation in this way, from suppliers to end customers, means that VSM offers a fresh view enabling the place(s) where value creation really occurs to be identified.
Modelling diagrams of this kind are not new, the book Installing Efficiency Methods by Charles Edward Knoeppel in 1915 included them, but they only became popular in the 1980s when Lean Management enjoyed a boom. While the “VSM” abbreviation was yet to be invented, the technique was a mainstay of the Toyota model’s success, although for once it wasn’t the Japanese firm that had actually created it.
Definition of value stream mapping
Value stream mapping is a representation of all the flows of materials and information for a process within an organisation. Historically used in goods manufacturing, to trace every movement of materials and components, it is widely used nowadays for any and all types of process. VSM can indeed be applied to a broad sweep of activities, whether in manufacturing, logistics, software development, healthcare, the services sector, or national and local government. Multi-purpose by its very nature, it works impeccably in every organisation studied, and is consequently a vital technique in continuous improvement processes.
The visual representation uses a consistent set of symbols to represent the various elements, which serves to highlight those steps that add value and those that, in contrast, do not. The removal of the latter can then be investigated. Mapping the value chain in this way delivers a number of benefits:
- At-a-glance understanding of how the organisation actually works;
- Identifying the causes of waste and bottlenecks;
- Increased production capacity without necessarily expanding physically;
- Uncovering opportunities for subcontracting or indeed insourcing.
Objectives and advantages of the VSM technique
One of the main benefits of using VSM is obviously the elimination of waste and sources of non-quality. However, by detailing every essential step in a process, the mapping mainly provides better understanding of how each step creates value for the customer. It accordingly enhances the Lean Management toolkit, because it is not really an additional optimisation technique, but instead an effective method for refocusing the business on what really counts for its customers.
VSM is therefore an excellent add-on to the Six Sigma method. The two methods differ in their implementations and can thus be used in different situations to foster the creation of a system offering the best possible performance. The Six Sigma method is of interest to those activities that generate waste, whereas VSM identifies activities that generate no added value versus those that are crucial and contribute to the performance of the business. Together, they can form the mainstays of a corporate culture and actively contribute to improving the organisation’s operational excellence to better withstand competitive pressure.
Used within a wider Lean Management approach, the VSM technique accordingly brings two additional benefits of great interest, as it helps to:
- Detect key areas for improvement thanks to the overview of processes it provides, making it easier to assess what changes are necessary;
- Establish a global improvement strategy intended to both correct problems directly at their source and also to reinforce those aspects that create value.
However, the cost in terms of the resources and time needed for the approach to really prove worthwhile must not be underestimated. Staff absolutely must be properly prepared for the use of VSM so they are totally operational and the mappings produced therefore fully understandable by all of the organisation’s stakeholders. Do not overlook that communication focused on value creation in terms of continuous improvement is crucial above all else. The visual representations from VSM can thus quickly become educational resources helping to improve understanding of the changes needed and securing staff buy-in, thereby also contributing to the success of transformation projects.
To find out about best practice in delivering successful action plans, download our e-book without delay:
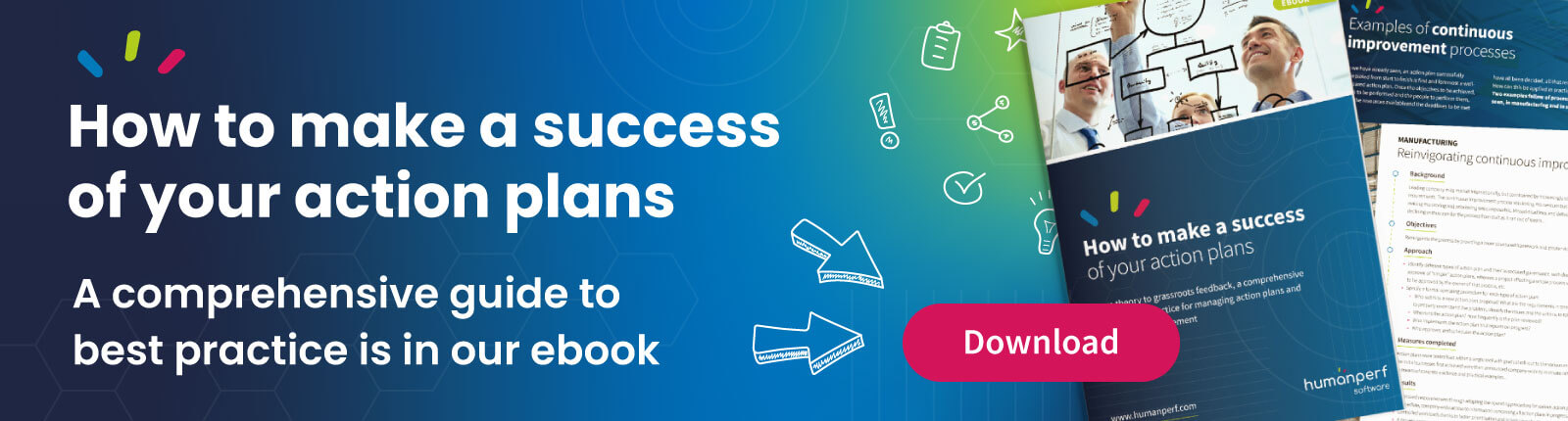