The QRQC (Quick Response Quality Control) method is probably one of the most powerful tools available to swiftly and permanently resolve quality issues encountered at grassroots.
Unlike other problem-solving tools, such as 8D, DMAIC or 5W1H, the QRQC method suggests a pragmatic approach intended to fix non-quality in as short a time as possible, directly in the spot where it was observed. It is a method primarily based on objective measurement, and acts in such a way as to prevent the problem occurring again. Let’s take a look at this very popular methodology.
The six key points of the Quick Response Quality Control method
While the origins of the QRQC method are sometimes ascribed to the Toyota production system set out by Taiichi Ohno and the resulting Lean Management practices, it was really applied in the 1990s by the Japanese firm Nissan. Its objectives are very clear, and could not be more pragmatic:
- Always send compliant goods to customers,
- Eradicate recurring incidents,
- Improve productivity,
- Make teams accountable.
To achieve these objectives, Quick Response Quality Control is based first and foremost on facts. Not assumptions, not hypotheses; this method is built on direct, tangible observation by persons directly involved in the place where the problem arises. In contrast, while designed for use on the shopfloor, it also serves to resolve problems for the long term, through its six key stages:
- Go to where the problem occurs and observe it.
- Examine all parts, bad and good alike, and outputs to understand exactly where the problem comes from.
- Talk to people, using only facts and real data.
- Deliver a quick response to the end customer.
- Stay logical and factual to find the problem’s real root causes.
- Explain to other people and collect feedback to learn by doing.
The QRQC method consequently improves self-checking and strengthens the quality approach at every stage in the process. Although all employees are involved, the manager takes ultimate charge over the method, and should also ensure that end customers are satisfied. The manager trains and leads employees in the QRQC mindset so as to fully embed it in the culture, in such a way that everyone sees problems as opportunities for improvement from that point onwards.
QRQC method: a management method based on escalation
To guarantee a quick reaction, a deadline is given to supply a response to the problem. Once the deadline has passed, if no viable response has been supplied, the issue is escalated to the next line management level, which in turn has a deadline to meet, and so on.
This fundamental principle means the right level of the organisation is involved in resolving the problem, and therefore in the continuous improvement process. Escalation is directly linked to the problem’s complexity. The more the unresolved problem entails cross-functional causes or the greater the number of people required to fix it, the faster is the escalation. The same applies to the budget and resources allocated to remedial measures; the larger they are, the higher the resolution is escalated.
What are the points to watch to ensure success?
By speeding up interaction between management and operational staff in the event of problems, the QRQC method has shown it can deliver significant results. Considerable time is in fact saved in problem resolution simply by involving employees and giving them responsibility. In addition, besides operational staff, support and cross-functional areas can also be of assistance, and so operational excellence can consequently flourish within any business.
However, there are some points to watch if the full potency of the QRQC method is to be leveraged:
- Do not under-estimate the necessary workload - the QRQC method requires time and energy for all employees to appropriate it.
- The procedure must be organised and run so that all stakeholders are involved over the long term.
- Concentrate on the human aspect and not only the production side; the method only delivers results if all concerned are properly involved.
- Have a view of the entire ecosystem to ensure all those involved in the problem are involved in the solution, including external parties such as suppliers.
To find out about best practice in delivering successful action plans, download our e-book without delay:
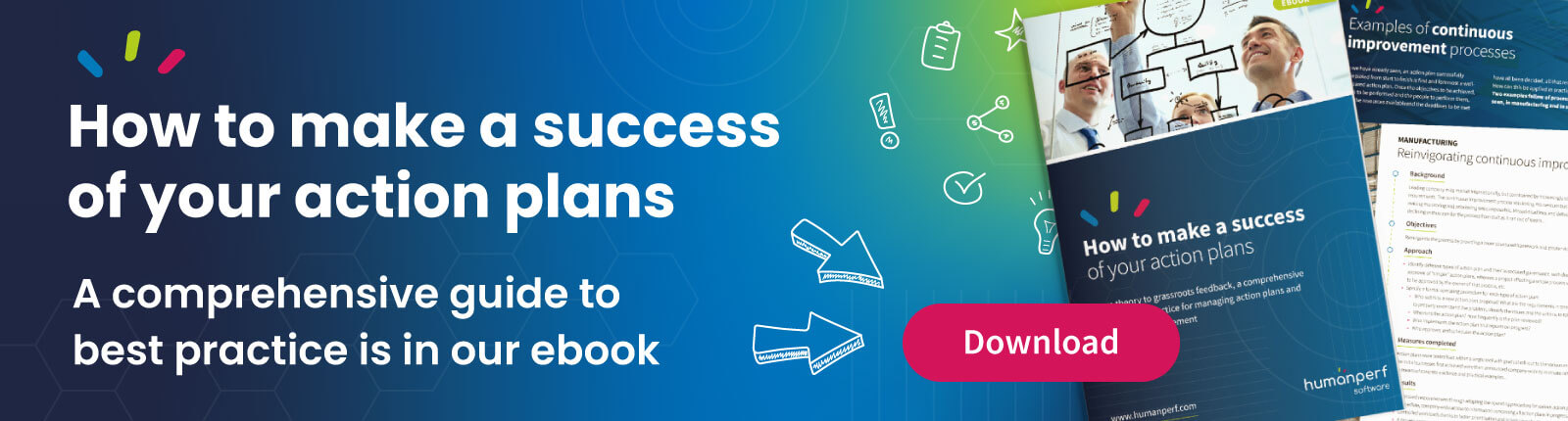